Frequently Asked Questions (FAQ)
What size parts can you process?
Our clear anodizing capacity is 58" X 42". Dyed coatings capacity is 58" x 42". Hardcoat capacity is 58" x 42". Passivation capacity is 48" x 42". Non-chromate conversion coating capacity is 58" x 42".
What Mil Spec Can you comply with?
We comply with most manufacturing & commercial specs as well as the following Mil Specs. Sulfuric Acid Anodize: Mil-A-8625 Type II Class 1 & 2, Mil-STD 171 7.2.1 & 7.2.2, AMS -2471 & AMS 2472. Hardcoat: Mil-A-8625 Type III Class 1 & 2, Mil-STD- 171, 7.5; AMS-2468 & AMS 2469. Passivation per QQ-P-35, ASTM 967, & ASTM A380
Do you offer expedited service? Can you help with rush orders?
Yes - we offer expedited service and priority processing. Contact us for details.
What is the difference between conventional anodize and hardcoat?
The conventional anodize (Type II) coatings can vary between .0001 - .0007 with 80% of the coating penetrating the base metal. The coating is transparent and can be left in its natural state or dyed in a variety of colors. We can process Hardcoating Anodizing or type III coating thickness range from .0005 - .0025. The coating color varies from a dark gray to a bronze shade depending on the alloy and can be dyed in a variety of deep shades. 50% of the coating penetrates the base metal and 50% builds-up on the metal surface. A .002" hardcoat will add a total of .001" per surface or .002" on diameter; therefore it is important to allow for these dimensions when machining a part.
What aluminum alloys can you process?
Most aluminum alloys can be processed successfully, however high copper aluminum alloys such as 2011 is not recommended for Hardcoat. High silicon castings may require special pretreatment procedures before processing.
What types of parts are suitable for bulk anodizing?
Bulk anodizing is only available for Type II (Conventional Anodizing) coatings. To maintain electrical conductivity during the anodizing process, parts must be held firmly together resulting in void areas on flat or large surfacing will show more defects than uneven surfaces.
What is your Non-chromate conversion coating?
Our Non-chromate conversion coating (NCCC) is an immersion process that does not require electrical conductivity therefore many items that are not eligible for bulk anodizing may be suitable for this process.
What is the difference between anodizing and your Non-chromate conversion coating?
Our NCCC is electrically conductive and less than .0001" thick. This is ideally suited for high volume cosmetic finishes.
What colors do you offer?
Having over 20 different dye stations on line, we offer most standard colors and our chemist can match shades to your needs.
What pre-finishes do you offer?
We offer Aqueous cleaners to remove oils and buffering compounds without altering the surface appearance. We offer both caustic and acid etch to produce a matte appearance on the surface. We also offer 3 bright-dip lines to chemically polish or brighten the aluminum.
What other coatings do you offer?
We offer post treatments such as ModernLube (a PTFE alternative) for lubricity, a variety of top coatings to enhance corrosion protection, and dry film lubricant to reduce the coefficient of friction. We also offer laser engraving.
Do you offer selective coatings?
Tight dimensional tolerance or electrical conductivity can be obtained prior to processing.
How should I prepare my aluminum prior to anodizing?
Unlike painting or plating, anodizing is a conversion process and will not cover scratches or deep surface defects.
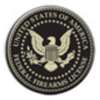
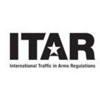
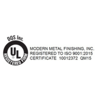
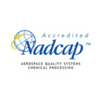